Welding and welding of plastics
Plastics
Plastics, or polymers, are materials that consist of synthetic polymers that do not occur in nature.
The following examples of types of such plastics are listed: synthetic of natural origin, synthetic of artificial origin, engineering, porous, fibre-forming, reactive, thermoplastic.
Welding
Welding is a method of joining non-metallic materials or materials that involves inducing the contact between the joined common grains of metal by recrystallisation and diffusion of the grains next to each other. For the welding process to be successful, the pressure, temperature and duration of the process are important. When joining parts, the most common temperature at which a good weld occurs is one that is close to the melting point.
Types of welding include:
- electric: resistance or spark,
- gaseous, e.g. made with an oxy-acetylene torch,
- frictional (friction of the contact surface occurs by applying pressure),
- thermite, involving the combustion of aluminium in powdered form together with metal oxides,
- electrical, used for machine components.
Welding
Welding is the joining of materials after they have been heated and melted at the joining point. As with soldering, a filler metal is added to the area, but this is not necessary. The heat used in welding generally comes from the welding arc, which is created by the current generated by the welding current source.
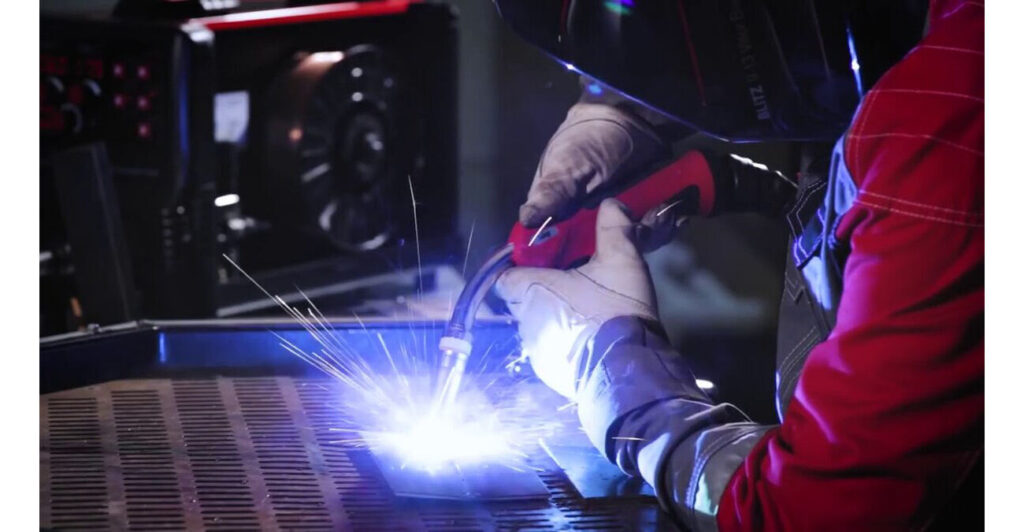
Welding of plastics
Plastic welding is a process designed to join parts made of thermoplastic materials. When two plastics are heated and pressed together, a small piece of material is plasticised and, once cooled, the joint becomes hard and durable. This heat can come from outside, e.g. with a welding machine, but also from inside, e.g. with hot air. Plastic welding is very familiar with pipe welding.
The basic methods of welding plastics are::
- butt-end,
- couplers,
- electrofusion.
Butt welding is used to join pipes with large diameters. It is a safe proven method of joining plastic fittings and pipes by applying the correct temperature to join two components using mechanical pressure to form a homogeneous joint.
Sleeve welding, also known as polyfusion welding, involves heating the end of the fitting and the pipe to the correct temperature using a socket welder and then mechanically pressing the joint together. The correlation of the end and fitting and the polyfusion tool achieves such strength that it is able to produce a strong joint.
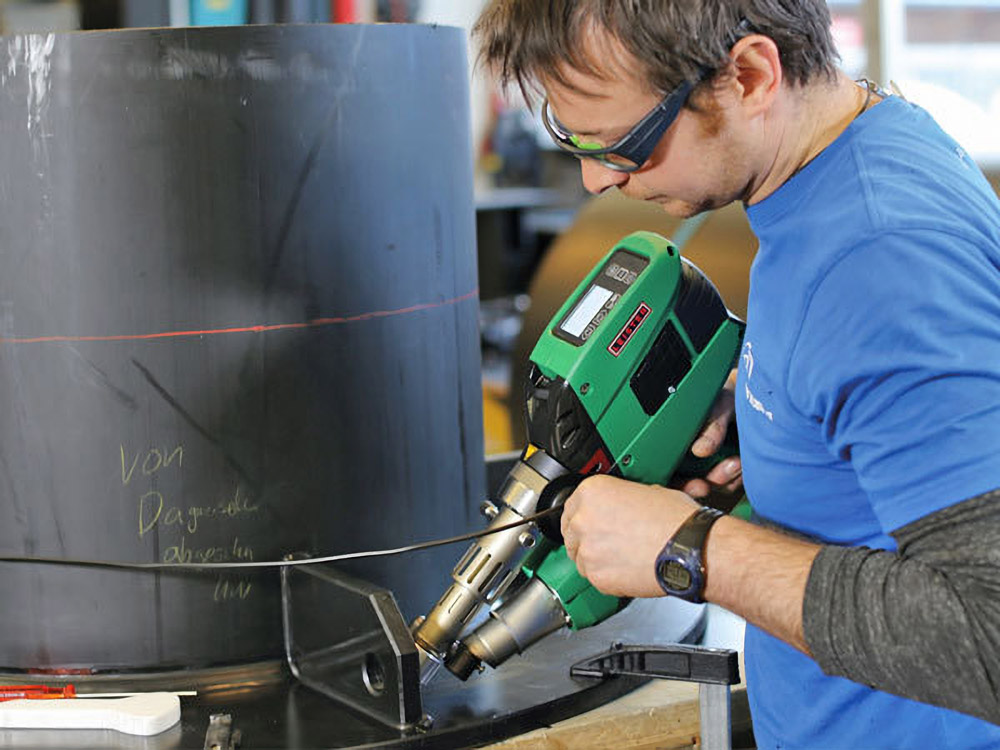
Electrofusion welding involves the juxtaposition of polyethylene pipes using fittings equipped with built-in heating elements, preparing the welding site in advance. This involves transmitting electrical voltage to the fittings, which contributes to the melting of the polymer and subsequent fusion of the fitting with the pipe.
Welding of plastics
Welding plastics is considered to be the most commonly used method of joining thermoplastic components. It involves plasticising the juxtaposed surfaces and filler material using high melting temperatures and pressure, resulting in a permanent cohesive joint. It is recommended that for most welding operations, the material joining the plastic parts should be of similar temperature and chemical structure.
Welding of plastics is carried out by the following methods:
- welding with a solid component,
- radial welding,
- gas welding,
- dynamic welding,
- electric welding.