Fiber optic welding course
ERGON cordially invites you to a course in fibre optic welding, in which you will not only acquire theoretical knowledge, but also practical experience. We have been operating on the market for over fifteen years, which makes us professionals in our field and provides comprehensive services to our customers.
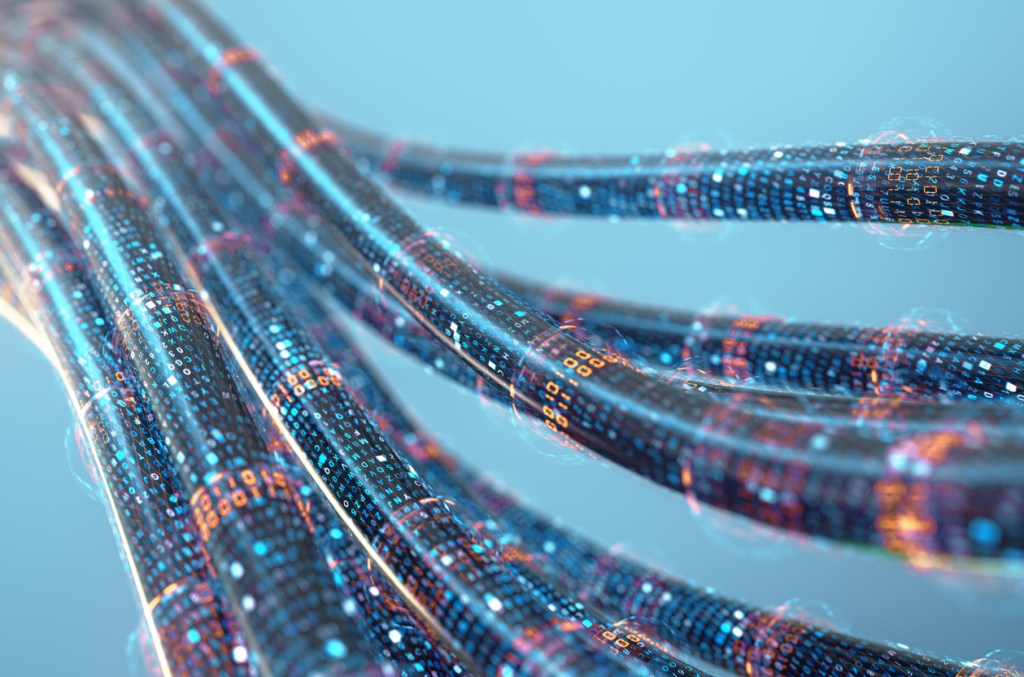
What will you learn?
During the training there are practical as well as theoretical activities, during the course you will learn:
- the basics of fibre optics,
- criteria for selecting a welder,
- use of fibre optic cables,
- measurement of optical fibre connectors,
- weld procedure,
- welder operation,
- steps in the execution of welds.

Through fiber-optic communication, we are able to obtain data transmission without interference, even up to several terabits per second, and thus, there is a great demand for fiber-optic welders educated in this field.
Therefore, this is the profession for you if you are a person who:
- appreciates precision,
- looking for a profession with a future,
- eagerly learns new skills or just wants to educate himself.
Why is it worth investing in training?
The main objective of our company is to provide our customers with first-class training services. Qualified methodologists and other people with many years of practice take care of the quality of training and the best possible satisfaction in all our facilities, which are located in Warsaw and other regions of Poland. However, we go the extra mile for you, we are mobile and organise closed training courses.
Working as a fibre optics welder
While the process of welding fibre optic splices is not in itself complicated, as we have the right tools to assist us, the welder is expected to be accurate and persistent in carrying out the task. Welding of optical fibers is nothing more than the bonding of wires, which includes fibreglass and plastic, in addition, through the process of heat using an electric arc, a permanent connection is obtained.
The instructors at our facilities place a very strong emphasis on education in assembly quality and the use of appropriate tools for the job. The basic equipment of a welder includes, among other things, welding machines, optical power meters, fibre optic cutters, kevlar scissors, and fibre optic connector cleaners. Why are the tools we use so important? There are a lot of offers on the market for the purchase of, among other things, welding machines, which seem to differ little from each other, and yet the same one is not used in every situation.
Types of fibre optic welders and their applications.
Welders centering the fiber core | Welders centering the fiber mantle | Centering welding machines to the real core |
There are two models here, centring to the geometric core and the real core. The initial system is used by most niche welders and, as with centring to the fibre jacket, will work well for really good quality fibres where the geometric core enters the real core. Positioning to the other is the system used in the best fibre welders. These types of splicers independently inspect the spliced fibre and are able to lay it perfectly to the real core, thus levelling attenuation to zero. | The most economical of the possible options, it allows the fibers to be matched to each other on the basis of their coats. Troublesome for these welding machines are the fibers of poor quality, because the core is not adherent in the place of the jacket. This connection has a slightly higher attenuation. | The best quality, but also the most expensive. The welder uses a method that can automatically recognise the types of fibre to be welded and arrange them relative to their real core. It features near-perfect attenuation characteristics. |
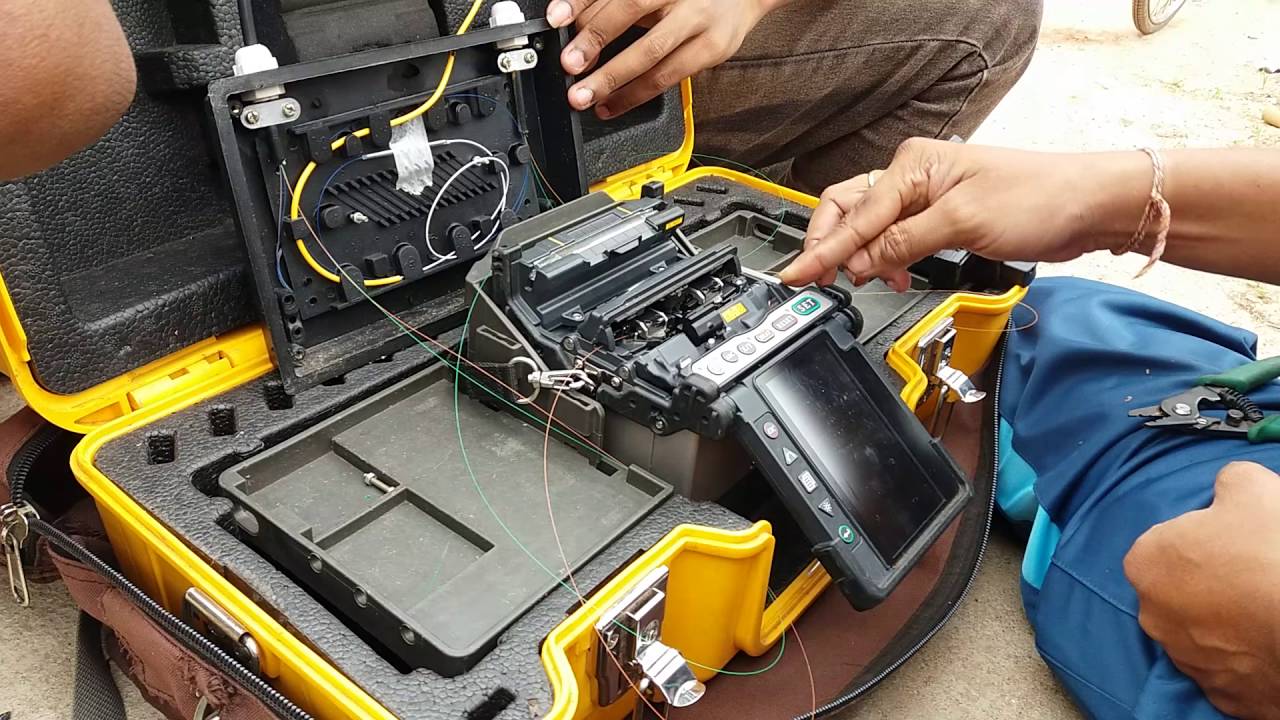
What are the steps to prepare for welding?
- At the very beginning, the appropriate diameter and length of the heat-shrinkable tube should be selected.
- Then remove the protective layer of the optical fiber with a stripper.
- The next step is to clean the fibre optic splicing junction and carefully trim it with a specialised knife with a diamond blade.
- And finally, preparation of the welding box, securing the cable with a heat shrink tube and welding the whole thing in the furnace.
The welding process takes place in 4 stages and is carried out by a welding machine. The first step that the welder performs is the careful positioning of the connecting cables with the exact centring of the fibres in relation to each other. The next step is to bring the contacts together with the correct arc current to achieve the desired temperature - this is to soften the cables and lead to a successful connection quality. The third step is to join the cables together using pressure at just the right time so that the wires are bonded. The final step is to release the heat of the fused wires so that they thicken and crystallise their structures at the connection point.
If you are interested in our offer regarding courses for the position of fibre optic welder, please feel free to call us. On our website you will find a tab where other training courses are also described.
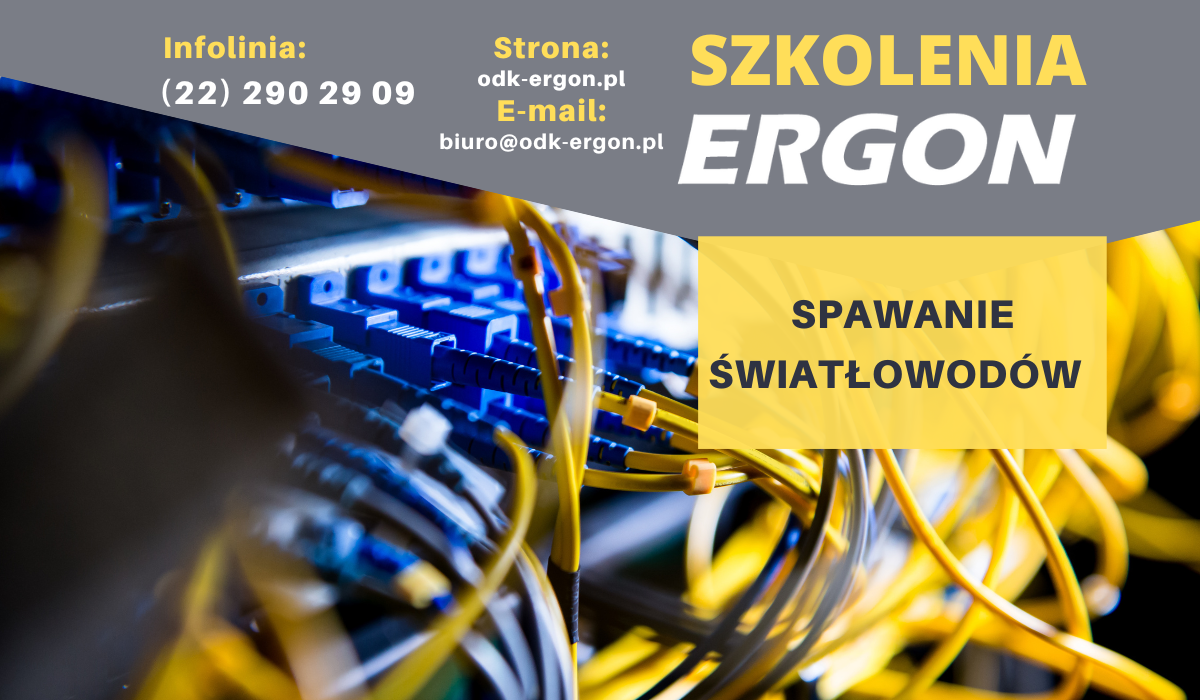